Mangal Industries stands at the forefront as a leading manufacturer of both standard and specialized fasteners, serving diverse Industries. Within the automotive sector, we cater to a vast array of critical applications, from axle assemblies to chassis components, from engine fixtures to transmission systems, our fasteners play pivotal roles in ensuring the structural integrity and operational efficiency of vehicles across various segments.
Industries We Serve
Products
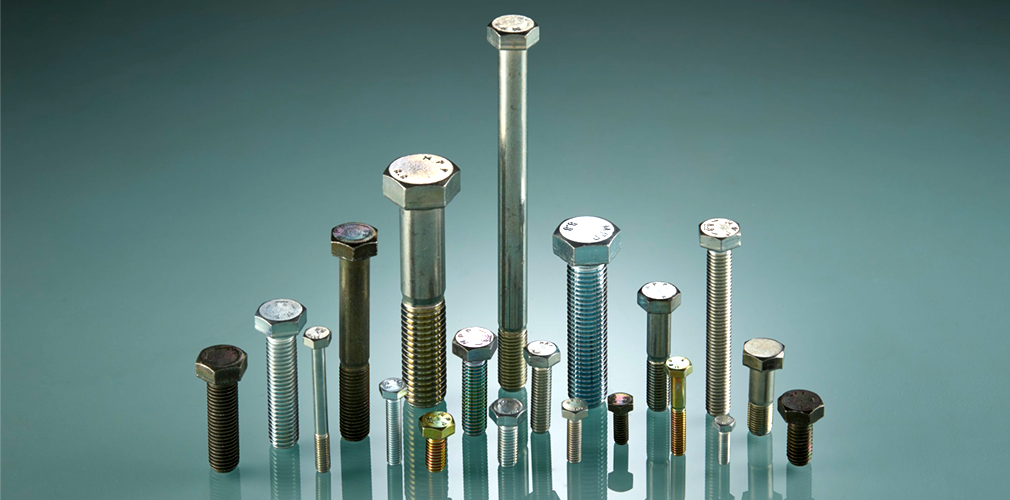
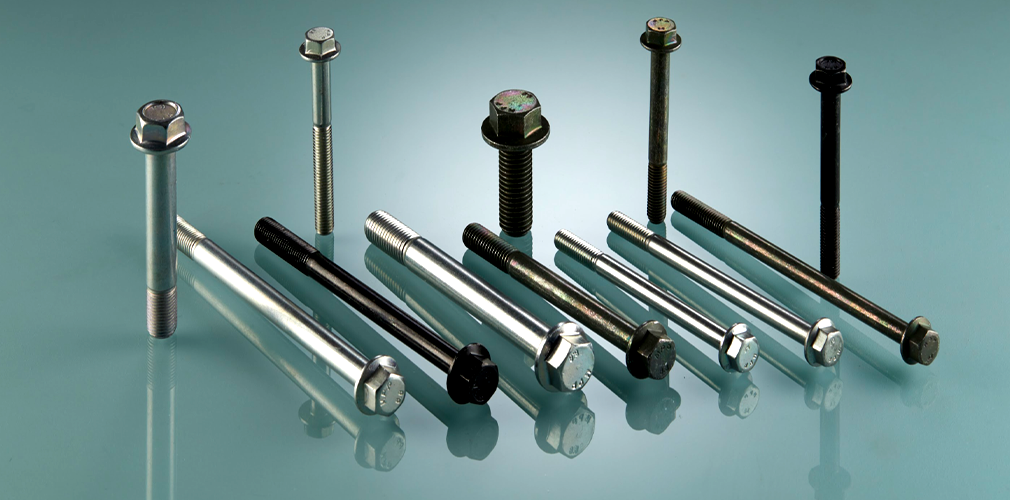
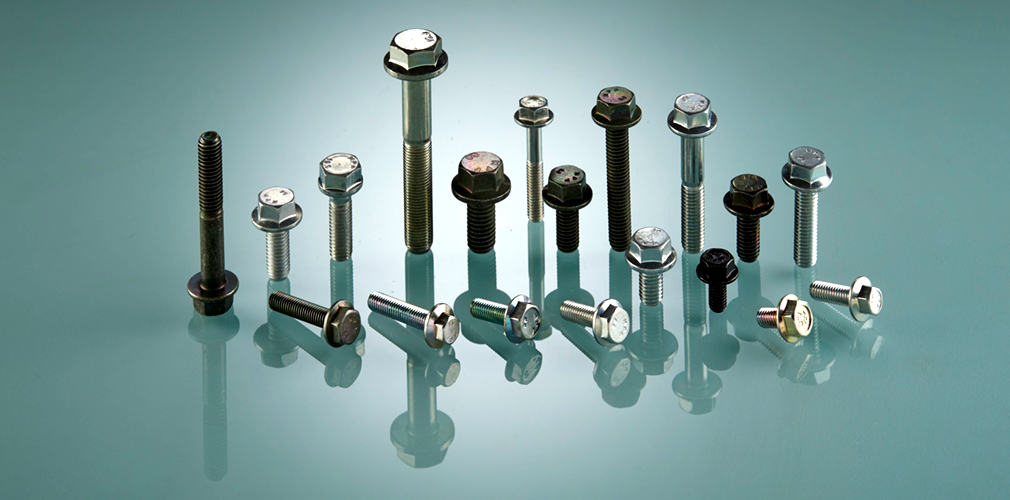
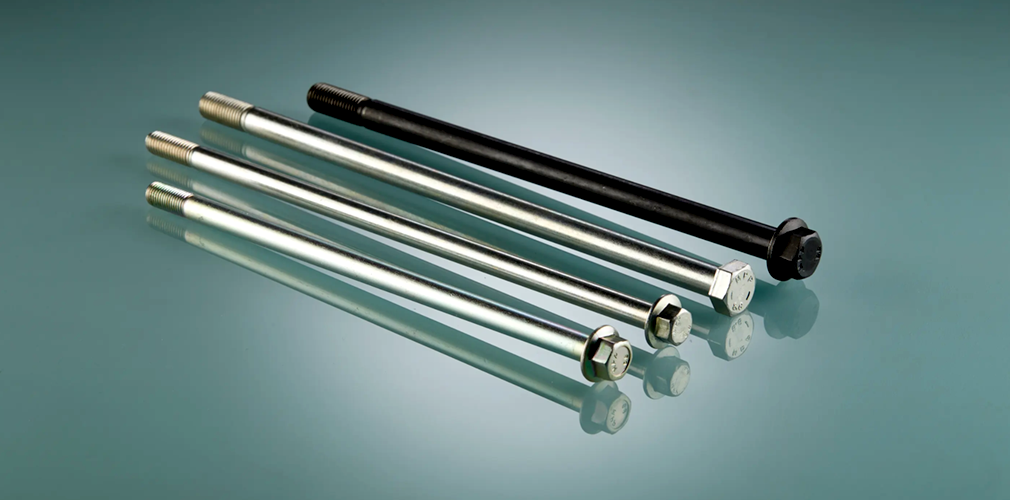
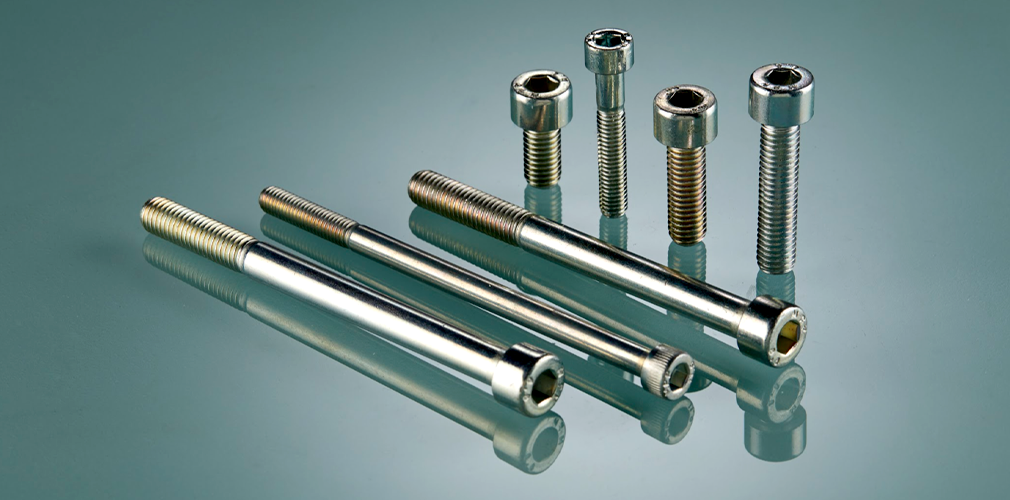
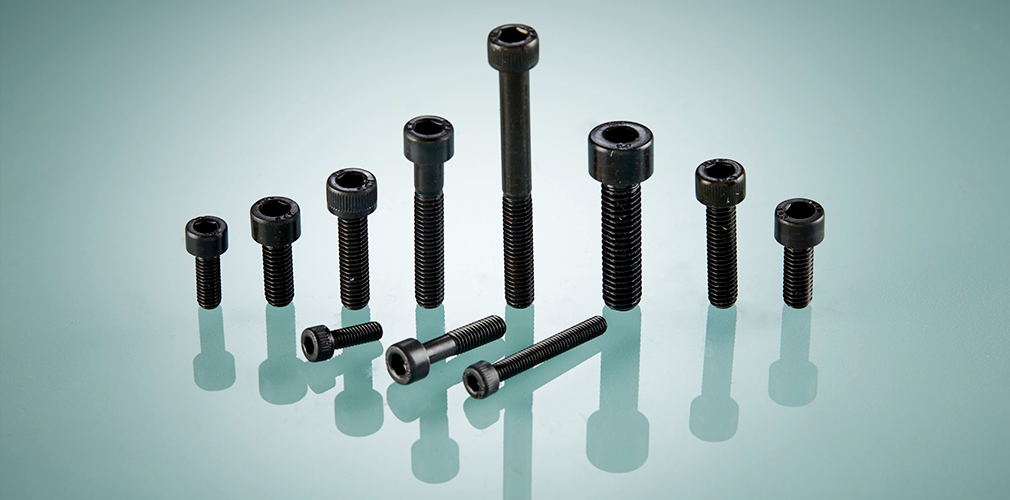
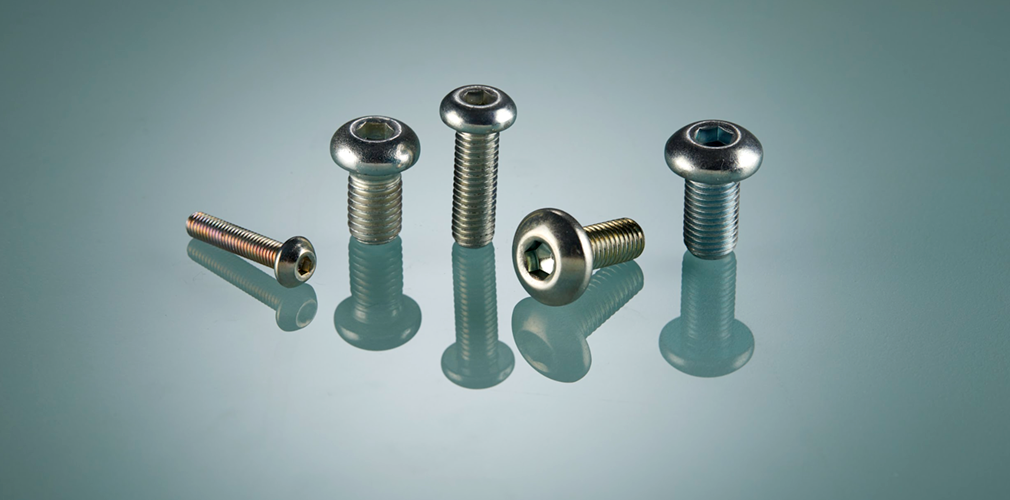

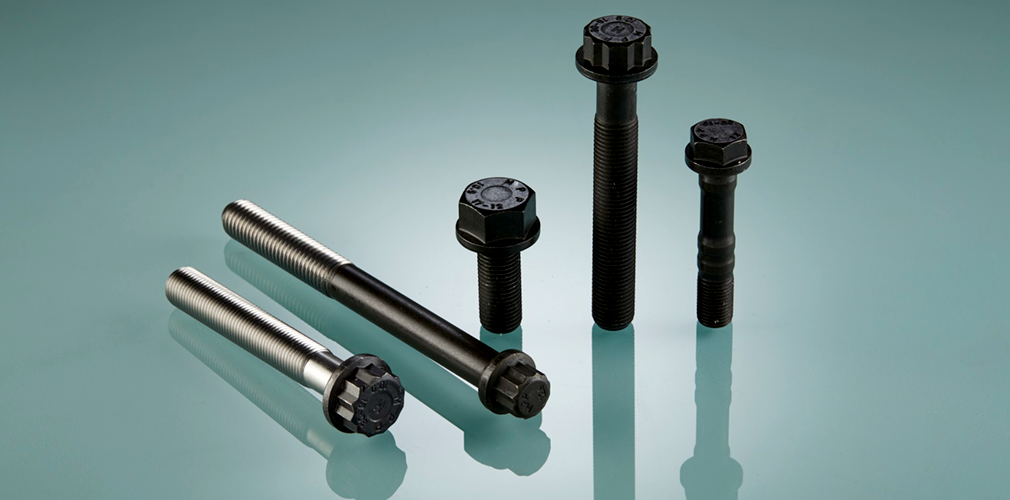
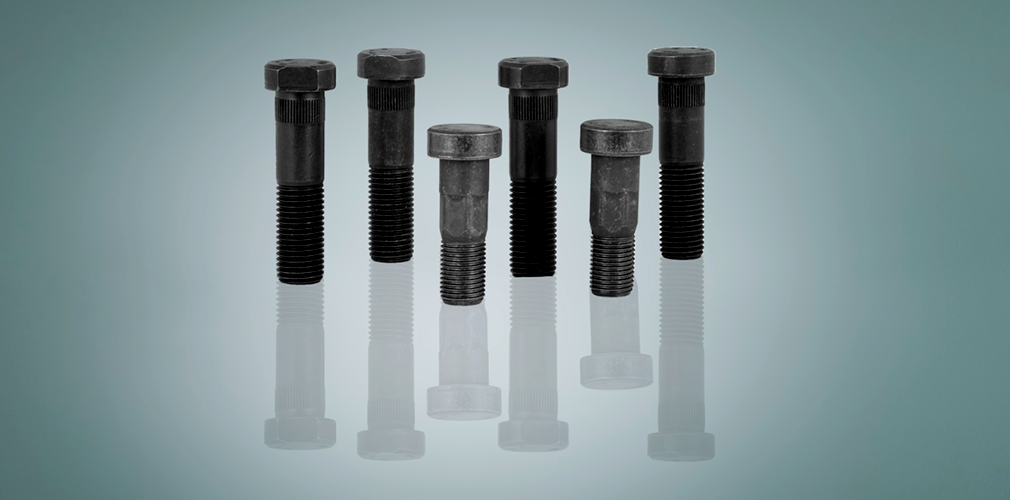
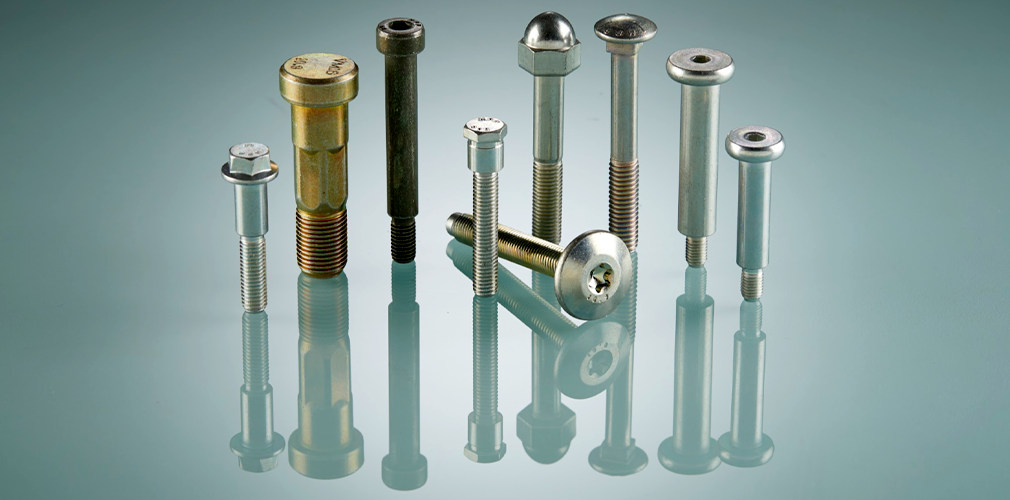
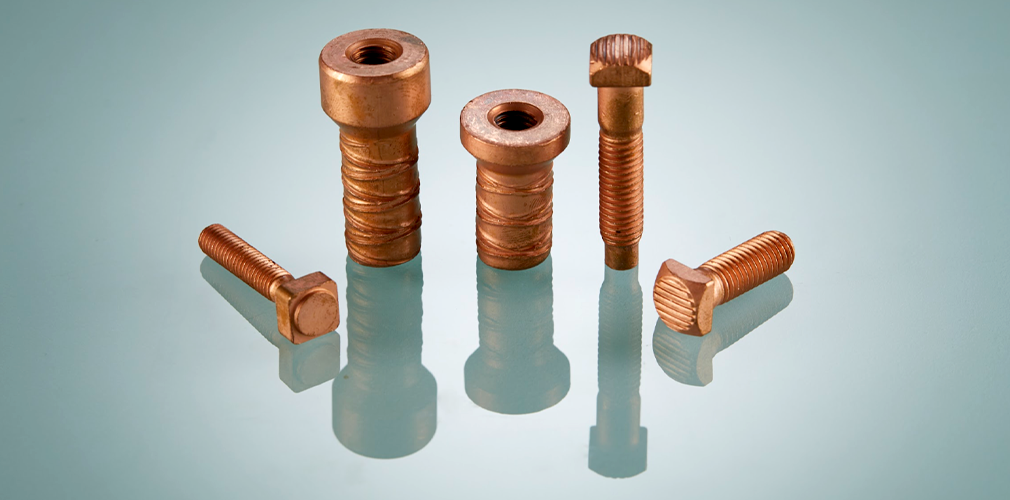
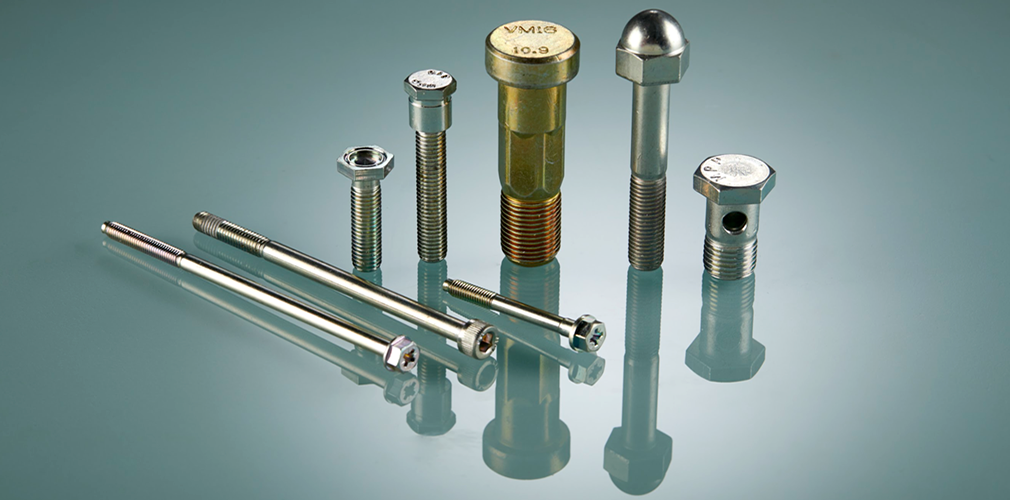
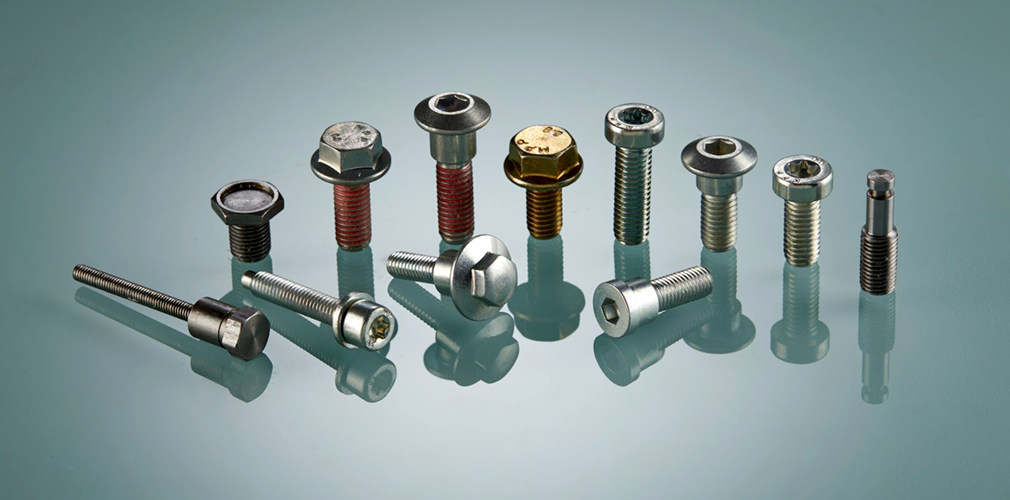
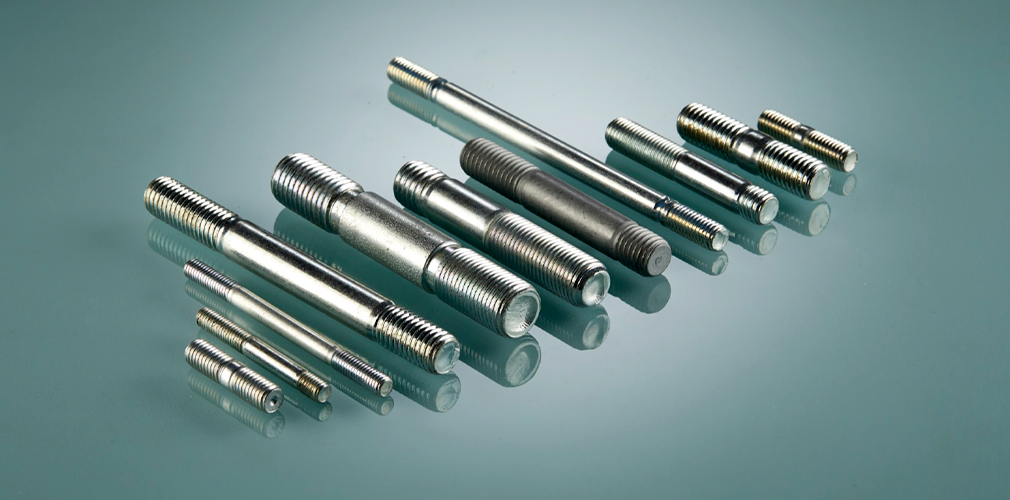
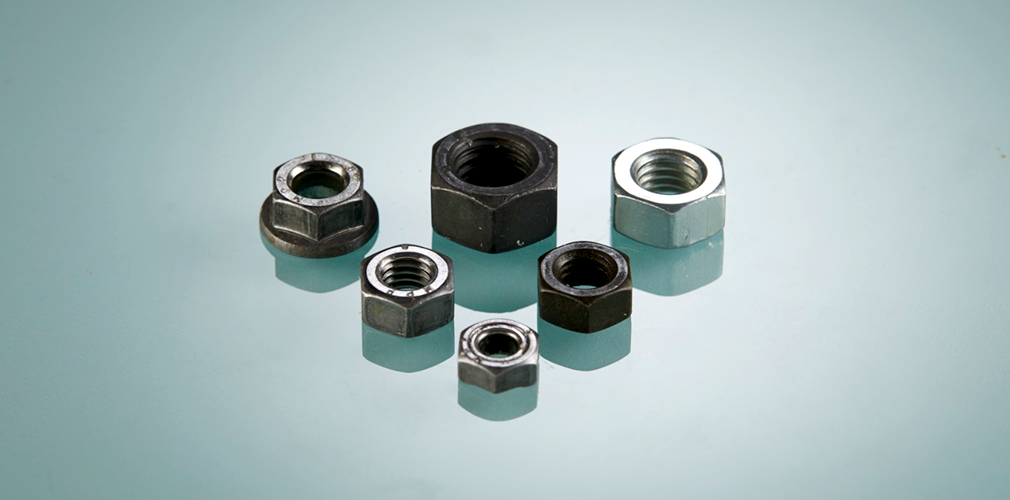
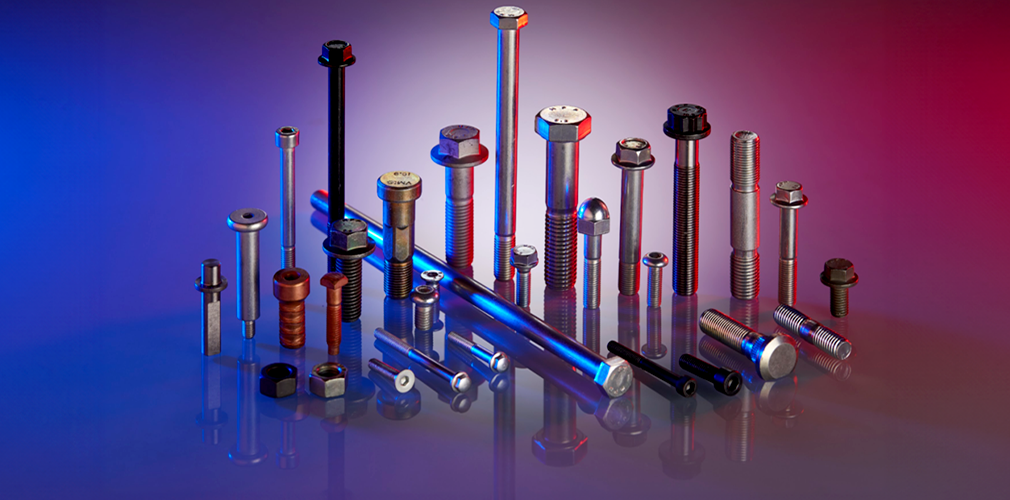
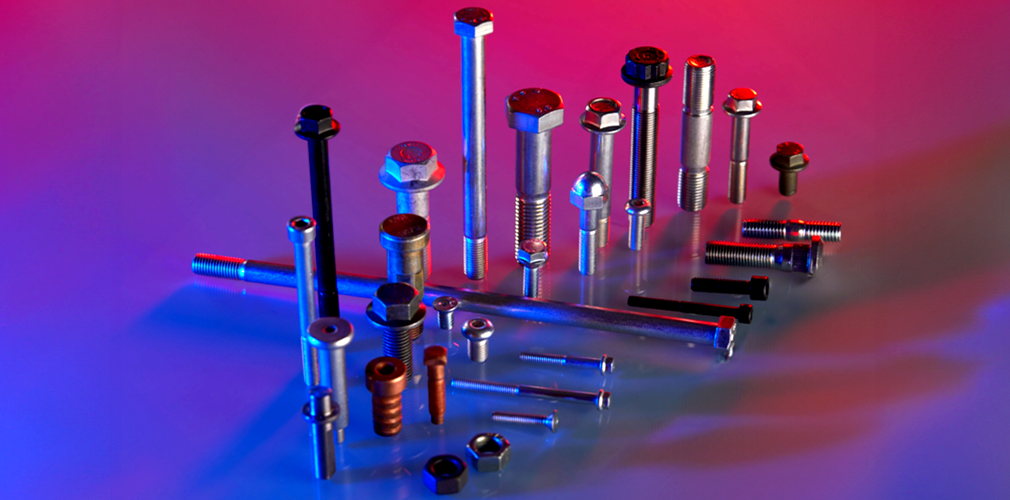
Technical Summary
Applications | Sizes | Grades |
---|---|---|
|
|
|
|
|
|
|
![]() |
|
|
||
|
||
|
||
|
State-of-the-art Manufacturing
With a capacity of 15,000 MTPA, our Fastener manufacturing processes have been meticulously honed and optimized over a decade to consistently surpass the quality, cost, and delivery expectations of our customers. We specialize in tailored solutions, carefully crafted to meet precise specifications and applications. Our collaborative approach, coupled with a keen focus on customer needs and value addition through design and process optimization, ensures successful product launches following APQP standards. Our fully integrated manufacturing facility encompasses wire drawing, annealing, cold forging, continuous heat treatment, secondary machining, finishing, and inspection – all under one roof.
Continual investment in cutting-edge technologies for engineering and manufacturing process optimization underscores our commitment to innovation. These ongoing advancements empower us to not only enhance our existing product lines but also introduce new ones featuring contemporary design and technology, on par with global standards. Additionally, our state-of-the-art plating facility, equipped with multiple lines, offers a diverse range of surface finishes tailored to meet industry requirements.
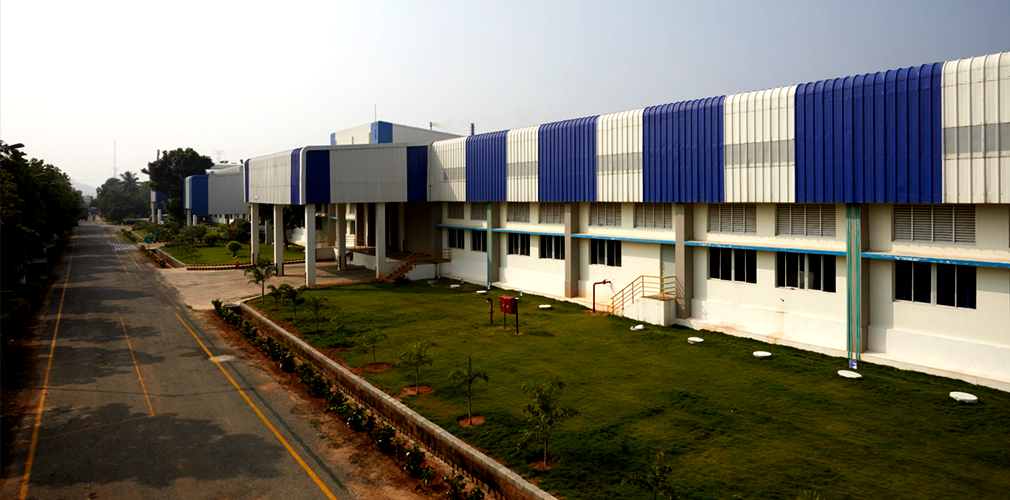
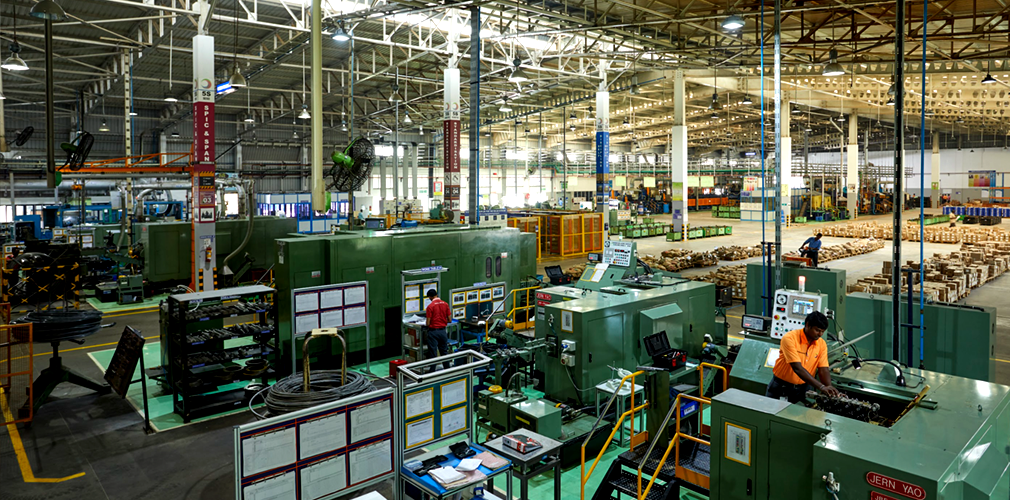
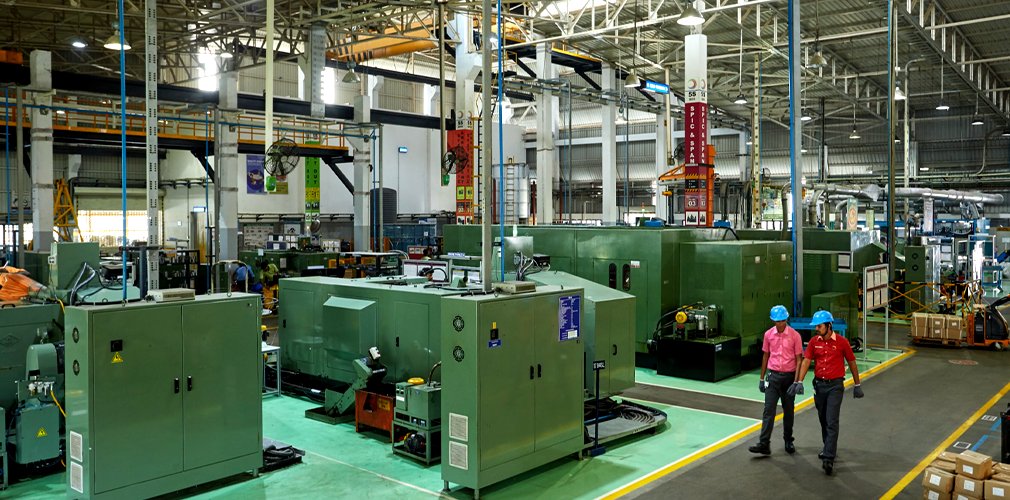
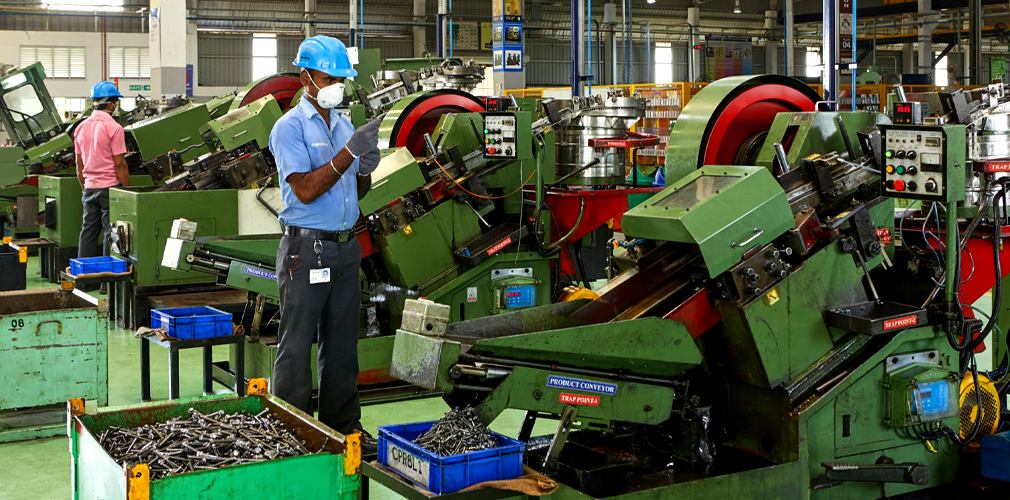
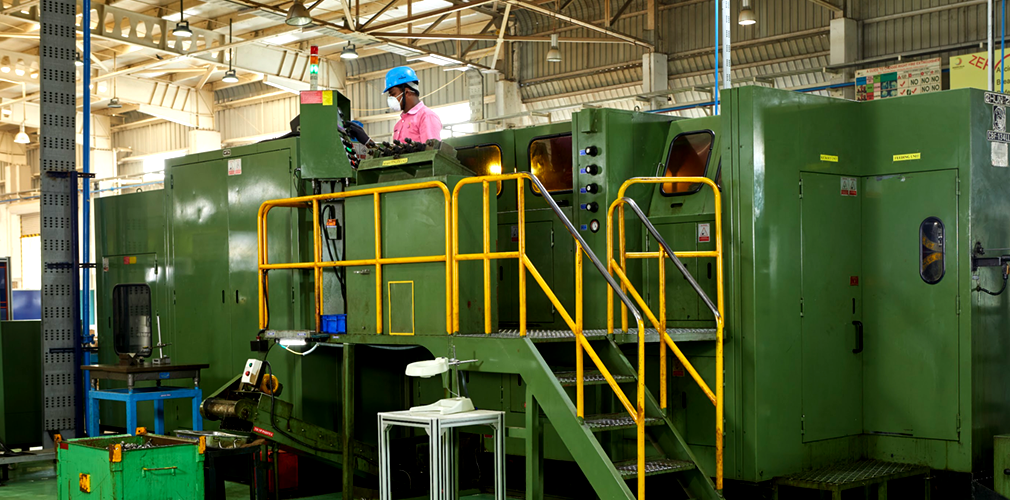
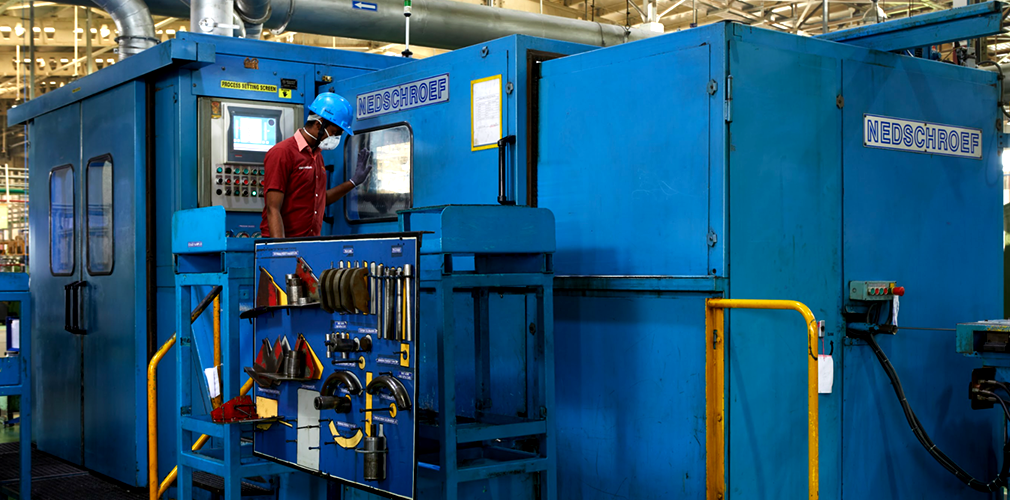
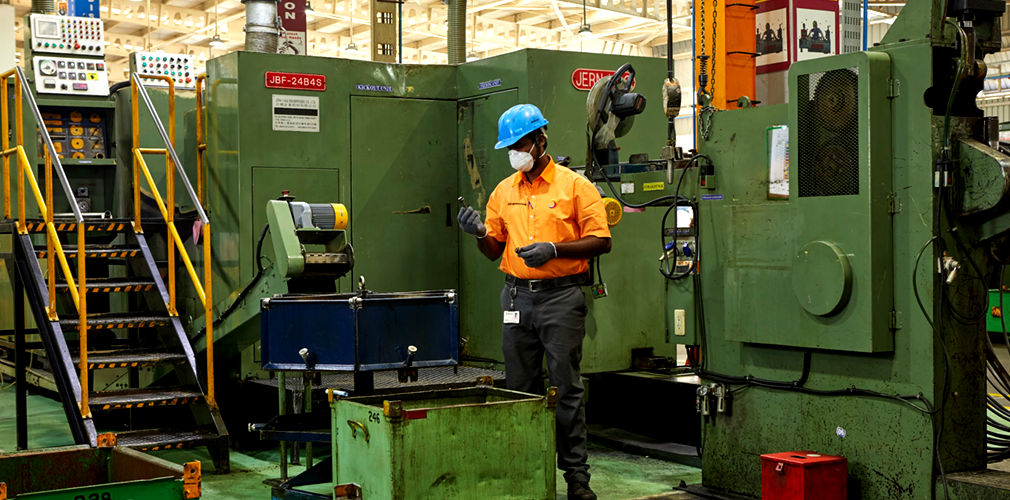
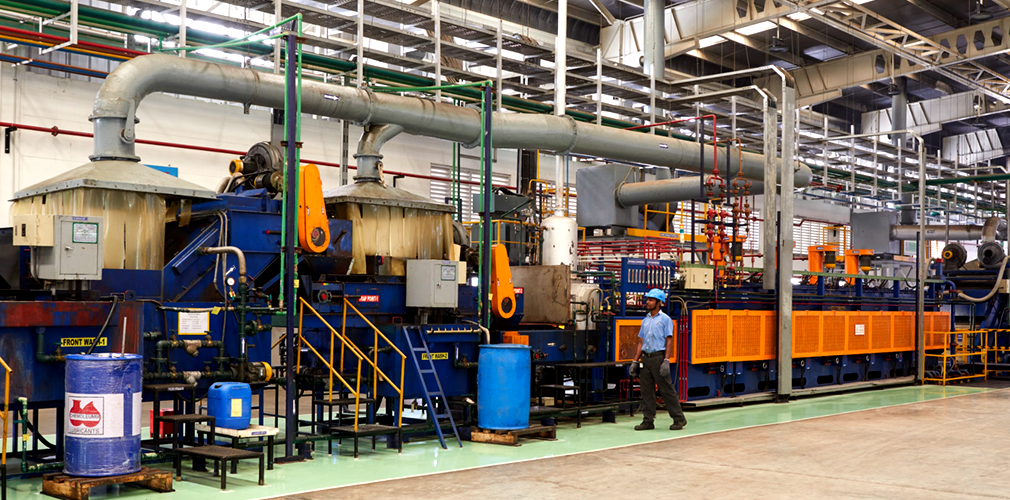
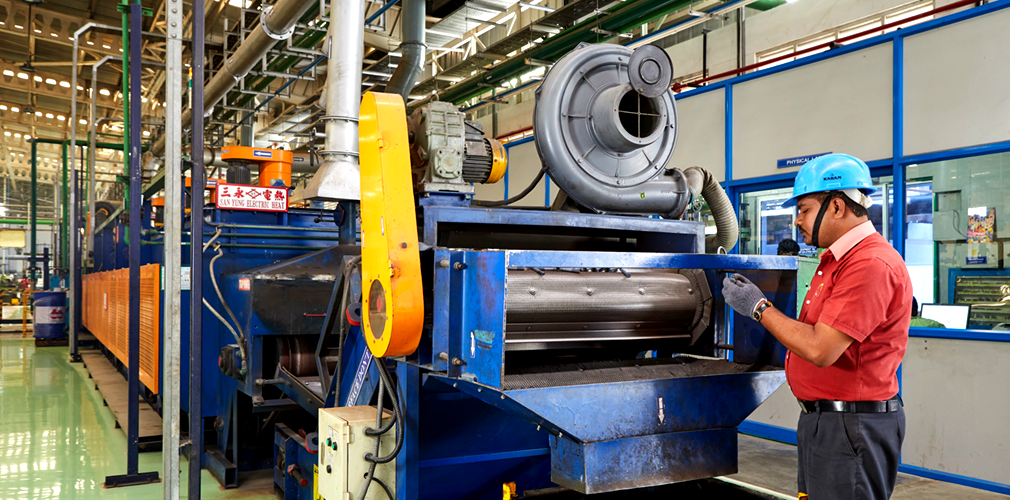
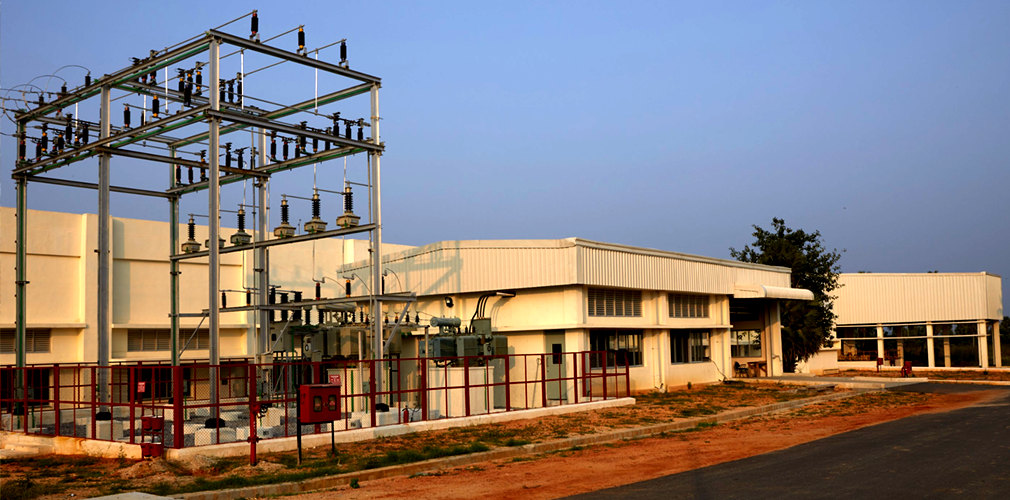
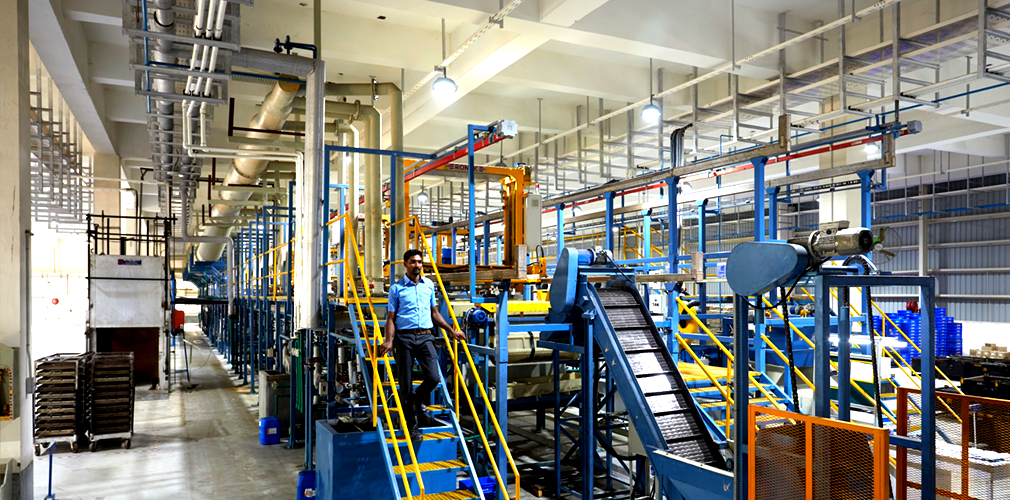
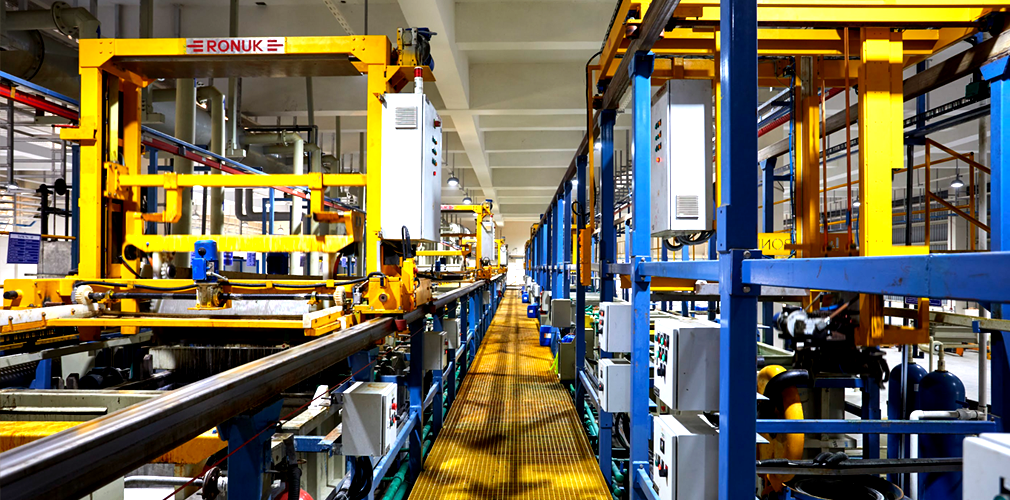
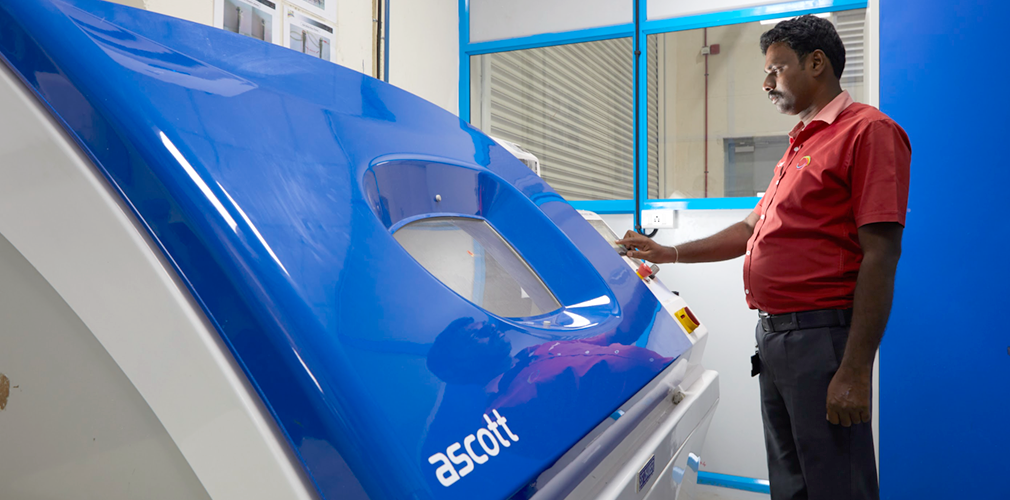
Fully Integrated Manufacturing Facility
From wire preparation to annealing, forging, heat treatment to a wide range of surface plating, all are in-house and integrated to ensure the highest quality and consistency.
Raw materials necessary for fastener production undergo processing at our wire processing facility, adhering to industry best practices. These materials are sourced from reputable suppliers in the form of coils.
- Raw material wires are initially gathered at the wire drawing stage.
- Rigorous inspections are conducted on the raw materials using various tests at the plant.
- Sequential processes including pickling, phosphating, drawing, and annealing are executed as per specifications.
- Once prepared, the wires, now ready for forging, are transported to the forging area.
Our cold forging machines, sourced from top international brands, boast state-of-the-art features that enable quick setup changeovers. The high-speed multi-station forging and rolling machines are equipped with load cell monitoring in each station and short feed sensors, ensuring superior performance and precision.
Thread rolling machines equipped with reverse thread sensors and auto conveyors are utilized to prevent rolling damages. Additionally, our arsenal includes high-speed flat and circular thread rolling machines, delivering precise outputs with efficiency and accuracy.
Heat treatment is a critical process in fastener manufacturing, as the consistency of heat treatment directly impacts the quality of the fasteners produced. At Mangal, we employ world-class continuous mesh belt furnaces equipped with SCADA controls. Our furnaces, sourced from Sanyung, feature advanced automation and are CQI-9 enabled, ensuring precise control and uniformity throughout the heat treatment process.
With multiple plating lines and continuous processing capabilities, we offer a range of surface treatments including:
- Zinc Phosphating
- Zinc Trivalent/Hexavalent Plating (Blue/Green/Yellow)
- Zinc Iron Plating
- ZAC and Zn-Ni
Our surface treatment plant, made by Ronuk, is fully automated and CQI-11 enabled, integrated with a SCADA system. Additionally, our effluent treatment plant is fully compliant, ensuring zero discharge.
Secondary operations, including turning, grinding, drilling, and facing, are meticulously executed using advanced CNC and centerless grinding machines within our state-of-the-art facility. Equipped with precision controls, these cutting-edge machines, along with our skilled operators, enable us to achieve unparalleled accuracy and consistency in our machining processes for their intended applications.
Engineering
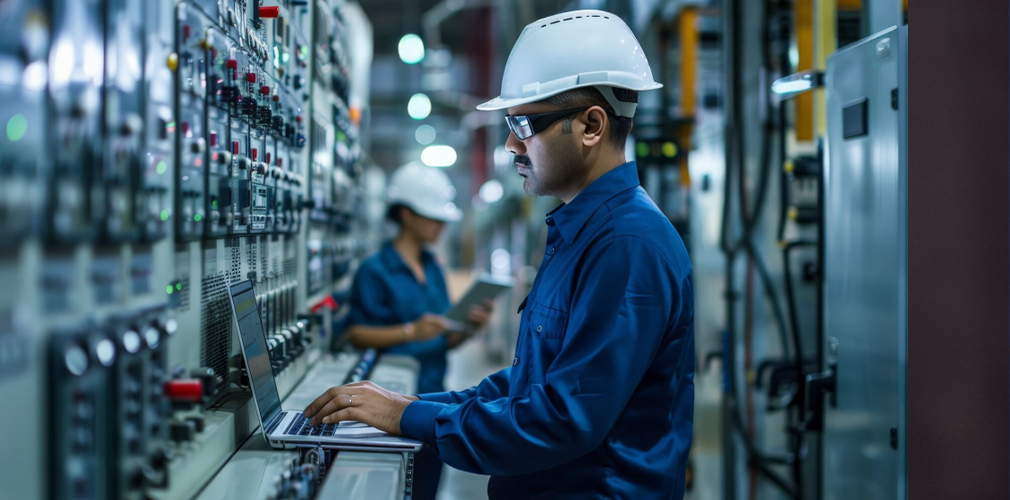
Embracing a collaborative approach, our engineering team actively engages in product design, innovation, and development, with a keen focus on application suitability, cost-effectiveness, quality assurance, productivity enhancement, and lead time optimization. We ensure that our developed products meet the exact requirements of their intended applications.
With advanced capabilities in product design, development, and manufacturing, we bridge the gap in application engineering within customer assembly lines, delivering unique value propositions tailored to our customers' needs.
Our in-house engineering team boasts exceptional capabilities in tool design, tailored to customer drawings and specific requirements. By prioritizing high productivity and extended tool life, we minimize the need for secondary operations.
Quality Assurance
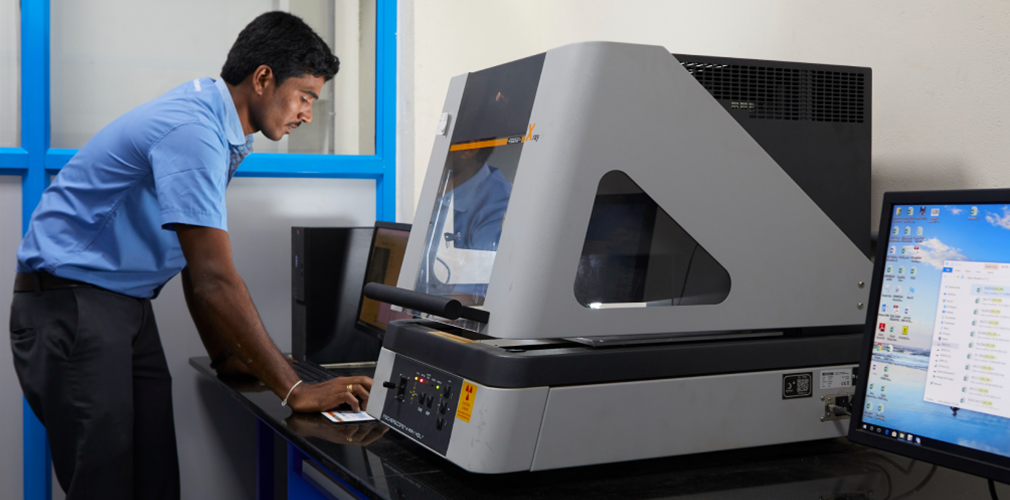
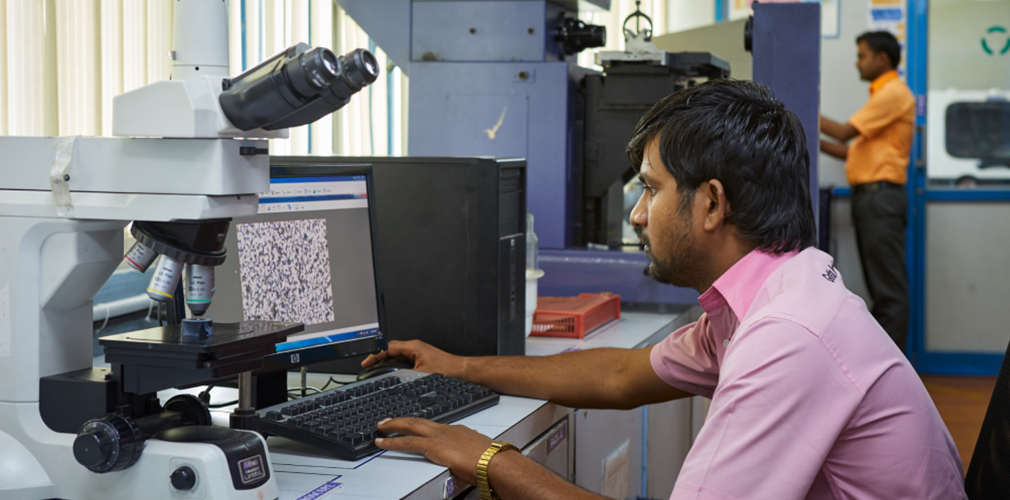
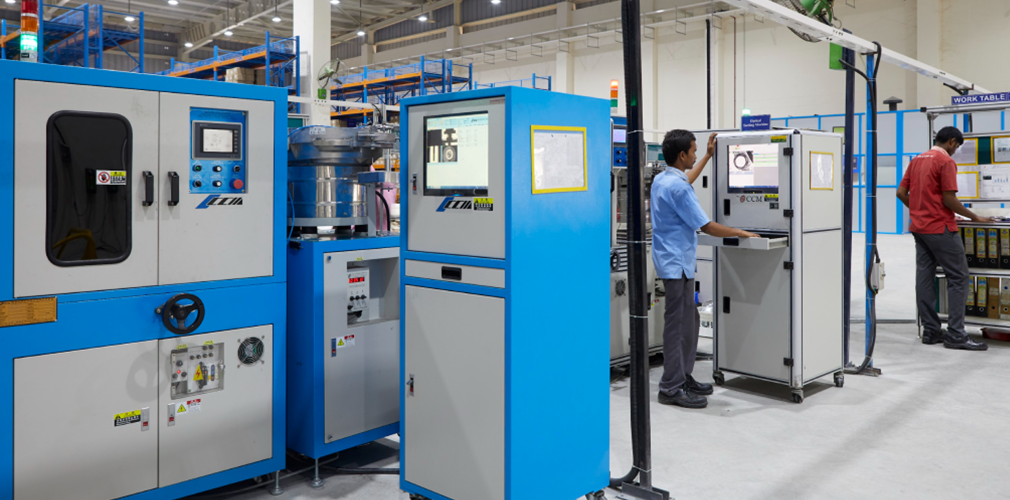
At Mangal, our specialized quality teams are devoted to monitoring key parameters, enhancing our performance in cost-effectiveness, quality assurance, and on-time delivery. Anchored by robust Quality Management Systems, our commitment to continuous productivity improvements ensures we consistently exceed our customers' expectations.
Our mechanical testing process is rigorous and comprehensive, spanning from raw material inspection to the evaluation of in-process components and the final product. This meticulous approach guarantees that our products adhere strictly to both national and international standards, ensuring superior quality and reliability.
In addition to our commitment to quality, we employ world-class inspection facilities for testing the physical and metallurgical properties of our fasteners. Utilizing auto-sorting machines, we eliminate manual errors and maintain consistency in our final products.
Our dedication to quality assurance extends further with our adherence to the 5S Sustenance and the TPM execution and driving continuous improvement through initiatives like Kaizens, Black Belt, Green Belt, and QCC programs.
Embracing digitalization, we've deployed TPM tracker IoT for efficient operations and implemented Blockchain technology for Tools, Die, and Moulds Management, further enhancing our operational efficiency and ensuring the integrity of our processes.
Proud Partnerships: Leading Brands Trust Us
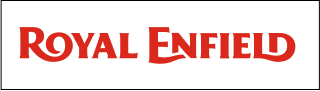
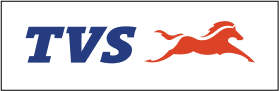
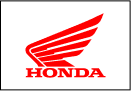
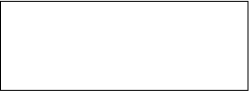
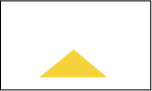
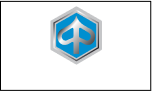
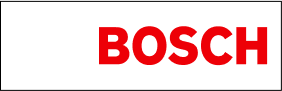
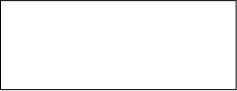
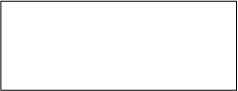
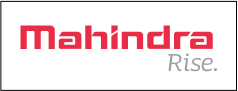
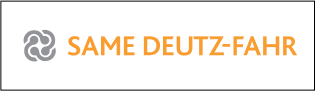
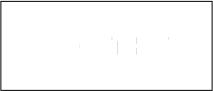
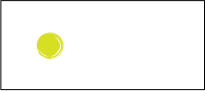
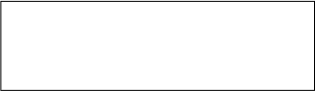
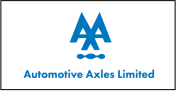
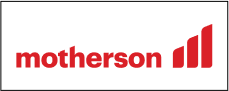
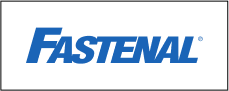
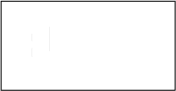
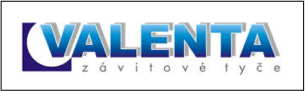
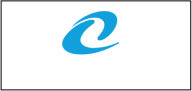

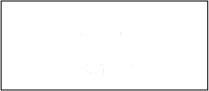
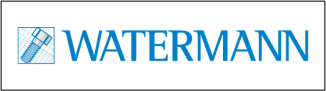
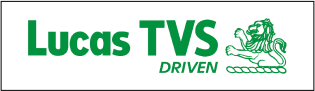
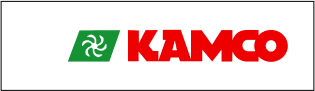
*The logos and trademarks are the property of their respective owners.